This Kenyan Entrepreneur Is On A Mission To Rebuild Urban Slums One Concrete Block At A Time
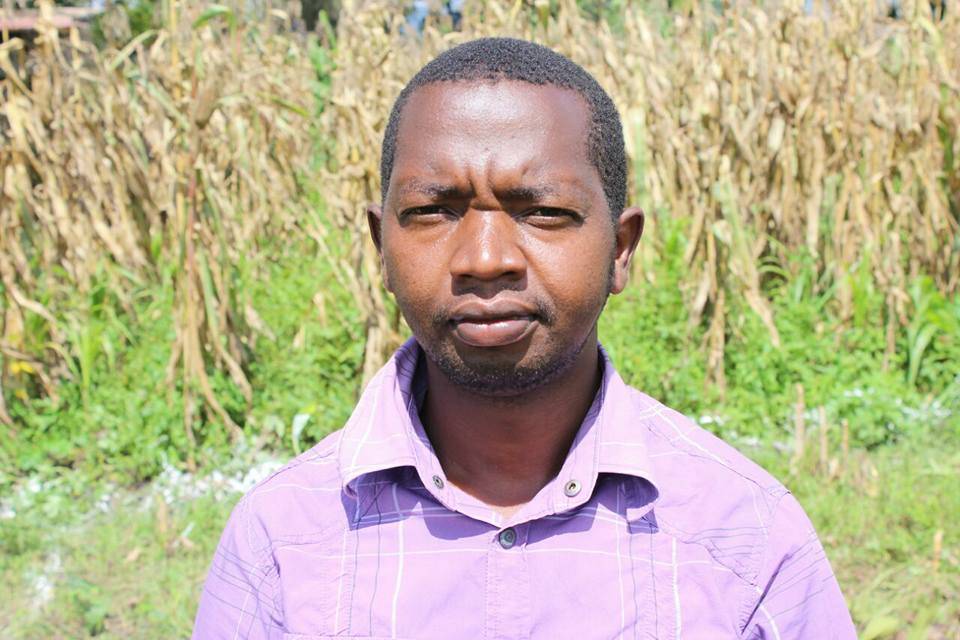
When James Mwangi left his house that morning, he probably had only one thing in mind. He had embarked on this trip solely to buy a bag of cement which would be used as input in the construction of a ventilation block.
But little did he know that the KSh 750.00 he had dug out of his pocket for one bag of cement will lay the foundation for what is now a company that may be well worth hundreds of thousands, or perhaps millions.
It was something of an unlikely start but these days, you’ll find him calling the shots at various busy construction sites on the outskirts of Nakuru Town. But James is not cut from the same cloth as the average site supervisor. He’s actually the boss at a fast-rising construction company that is making housing projects a far less-daunting prospect.
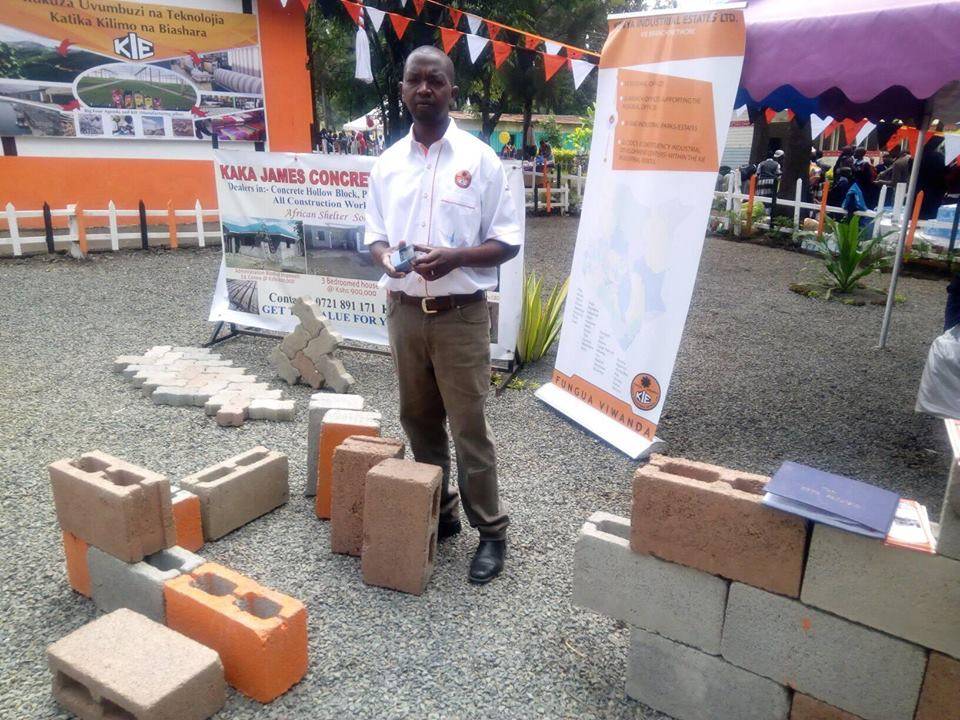
His company, Kaka James Concrete Enterprises, is carving a niche for itself in the Kenyan construction space by churning out low-cost building blocks using a special method known as interlocking technology. Through these efforts, “Kaka James,” as he is fondly called, is doing his bit to offer shelter solutions to residents of Nakuru.
The technology employed by James’ company significantly cuts down on the costs of constructing houses by eliminating some of the components that would otherwise crank up costs, and of course, without any comprise on the structural integrity of the erected buildings.
By compressing the building blocks with cement and waste from quarries with a hydraulic machine, what is turned out are eco-friendly building materials which make for a very affordable and appropriate means of taking care of the demand for decent homes that come on the cheap.
The new method, James says, is the key to providing affordable houses for millions dreaming of owning a home.
“This has enabled me to cut cost of the blocks and that is why with only KSh 70 K one can still afford to put up a single room instead of living in a mud house as two bags of cement are enough to join 400 blocks,” he enthuses.
After learning of the technology the same day he tried to purchase the bag of cement, James became quite interested in the opportunities it could afford. Convinced it’d make a viable enterprise, he was able to get his hands on a loan of KSh 50 K and that went into setting up the construction outfit.
Because of his endeavour, families that have occupied mud houses for several years in Nakuru are now beginning to dream about replacing those run-down homes to more modern structures.
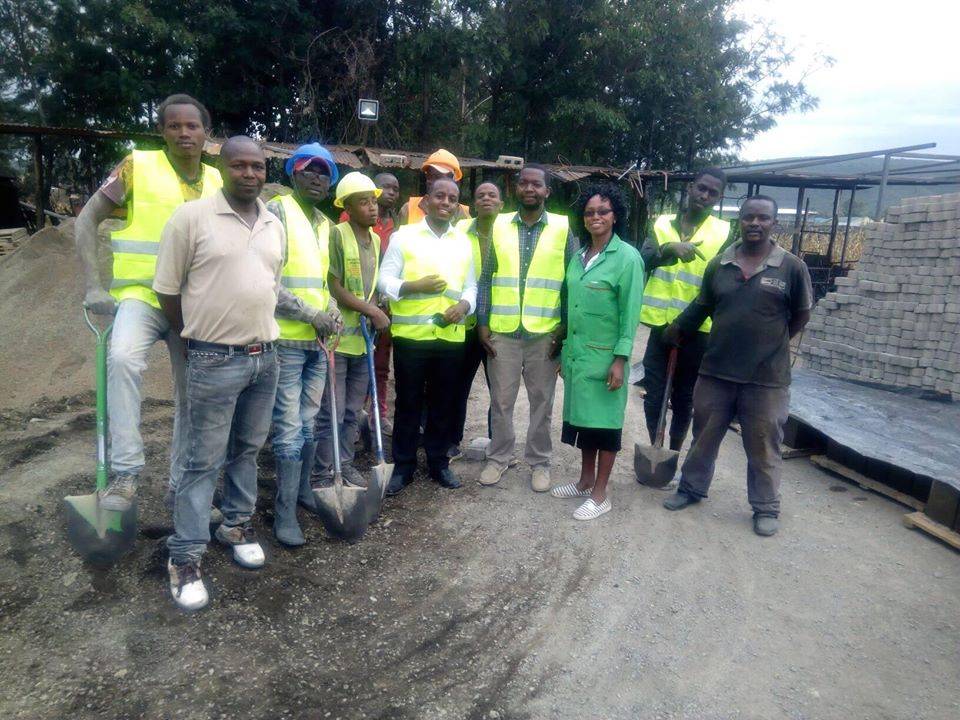
The Kenyan enterpreneur claims to have put millions of shillings into the procurement of the machines used for producing the blocks. At the moment, the company is believed to produce up to 2,000 blocks daily at a going rate of between KSh 60.00 and KSh 70.00.
“These blocks are light in weight which is good for storey buildings and besides they are thermal insulators and allow the warm air in the cavities to rise and exit the house,” he explained to Business Daily Africa.
James, who holds a diploma in architecture from the Kenya Industrial Training Institute (KITI) in Nakuru Town, is also a Certified Public Accountant who earned his scroll at Egerton University. Besides churning out low-cost building blocks, he has also ventured into the production of classic concrete paving blocks used in the groundwork for driveways and walkways, as well as hollow concrete blocks.
Currently, his products are sought after by schools, churches, private institutions, individuals, NGOs, an even the Constituency Development Fund (CDF).
He attributes the success he has so far achieved on dedication, resilence, patience, and a touch of compassion for the plight of poorly-sheltered families, having grown up in a slum himself in the Kiti area where he had to survive in a shack that housed a family of eight. He is also driven by the desire to satisfy the needs of clients and exceed his own personal goals.
James Mwangi hopes to spread the word about how housing projects can be made a lot cheaper than they are at the moment.
“A three-bedroom house which at the current market price can cost between Sh2 million and Sh3 million could easily be constructed at half the price,” he says. And according to him, his blocks can cut down on the cost of housing projects by as much as 45 percent.
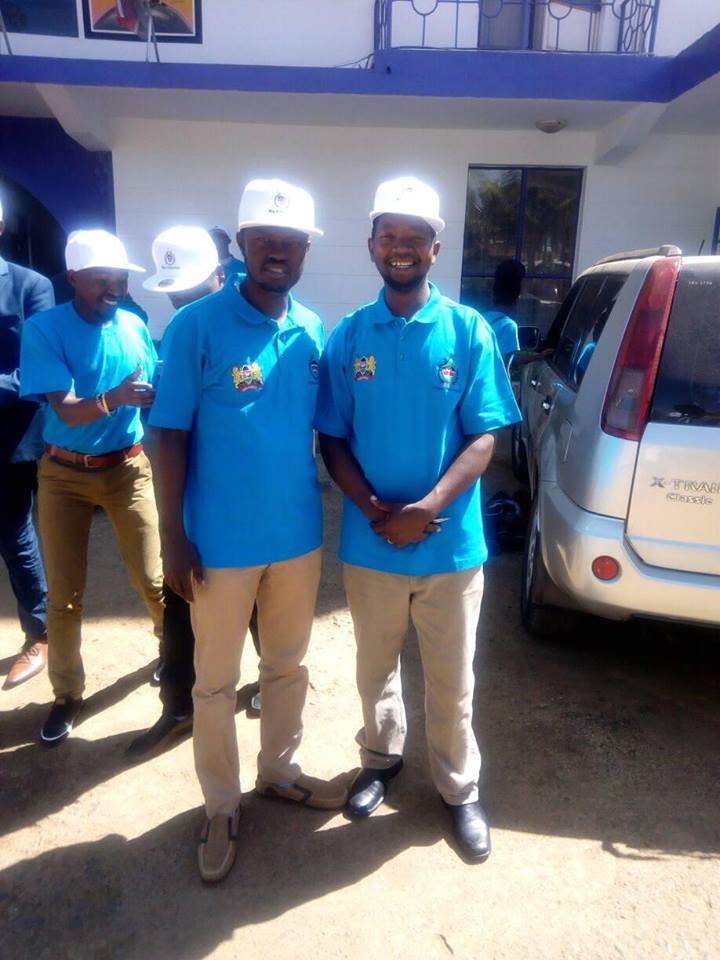
The Kenyan entrepreneur strongly believes that by leveraging this cheap, affordable technology, the cost factor in the construction business can be significantly dealt with, and many of the slums and other emerging settlement schemes in the country’s urban centres can be transformed in far more decent structures.
But it hasn’t been an entirely rosy affair for the Kenyan entrepreneur. When he started out with the business, he had just turned 27 and there weren’t many people who were enthusiastic about handing out construction tenders to someone who by “industry doctrine” could be deemed “inexperienced.” This made contracts hard to come by.
And then, there were financial constraints which were especially a bottleneck when those first big orders started to roll in. But it’s mostly a different story now as the Kenyan entrepreneur appears to be on a steady course and cruising too.
Image Courtesies: Kaka James Mwangi/Facebook